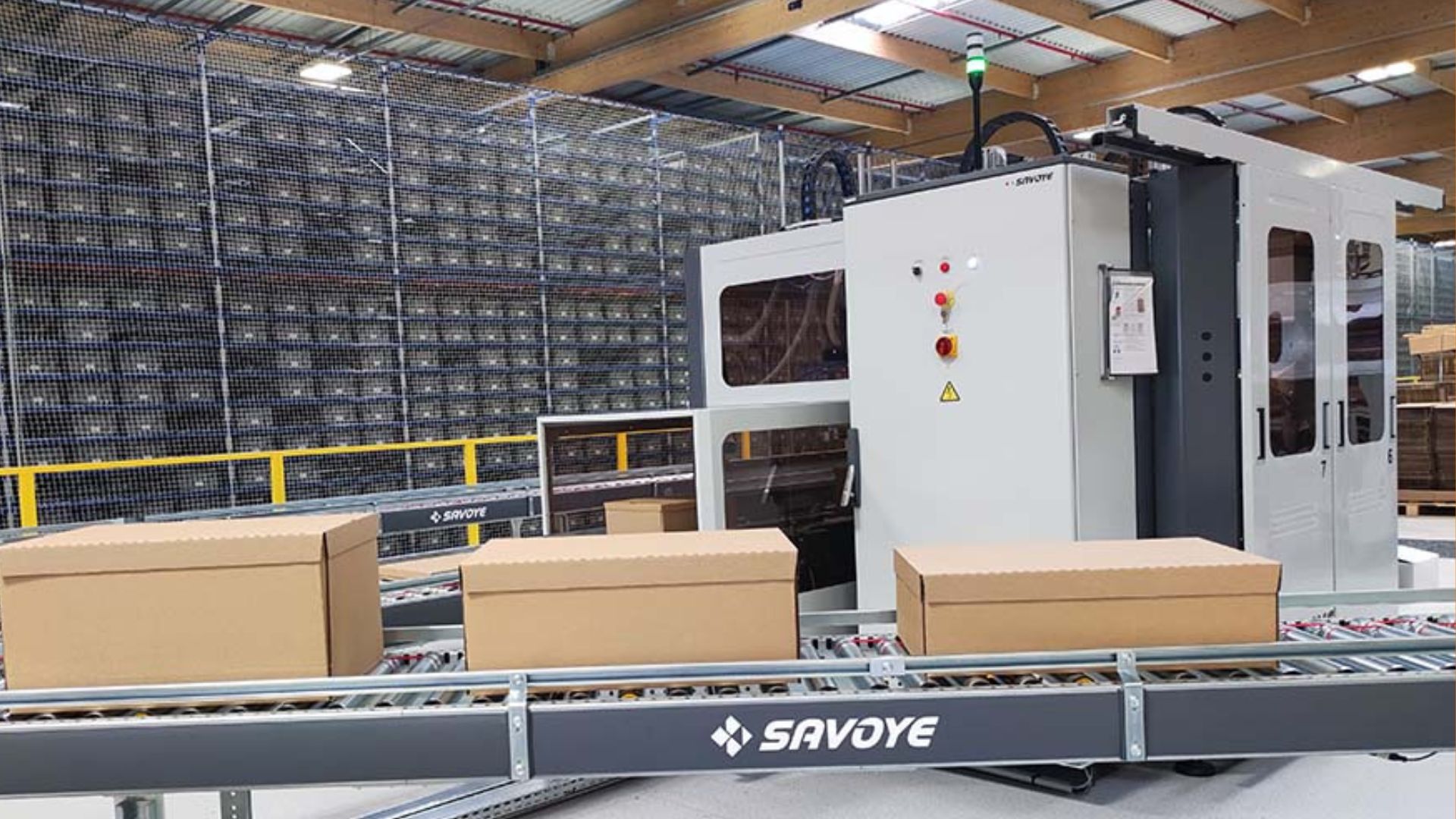
Le groupe bourguignon poursuit sa croissance, malgré les incertitudes conjoncturelles, dans sa spécialité, la gestion des flux internes des entreprises. Il capitalise sur sa capacité à en accompagner les mutations, voire les anticiper. Sa direction apporte son regard sur ces évolutions, à deux semaines du salon Euro Supply Chain à Mulhouse (Haut-Rhin) où Savoye exposera son offre, le 11 juin.
L’intralogistique, Savoye en est un acteur depuis plus de 40 ans, avant même donc que le concept se soit imposé sous cette dénomination dans l’univers de la supply chain, lorsqu’il en était encore à sa préhistoire. La fonction peut se décrire comme la gestion des flux à l’intérieur des sites d’une entreprise ou entre plusieurs sites, préalablement à l’expédition. « Nous intervenons dans la partie aval de la supply chain, jusqu’au chargement pour le transport, prestation que nous n’effectuons pas », résume Rémy Jeannin, le président du groupe basé en Côte-d’Or.
De cette spécialité, Savoye est devenu l’un des leaders mondiaux, fort d’un effectif d’un millier de salariés et d’un chiffre d’affaires en cœur de périmètre de 192 millions d’euros, réalisé pour moitié hors Europe : environ un tiers aux Etats-Unis au gré des exercices et 10 à 15 % au Moyen-Orient et en Asie. Le montant de 2023 est resté stable par rapport à 2022, surtout grâce à l’effet d’inertie dans le temps des commandes de long terme, dans la mesure où les nouveaux contrats sont, eux, restés stables l’an dernier, le contexte inflationniste ayant généré un climat d’incertitude sur l’évolution de la consommation.
Transversale aux secteurs d’activité par définition, l’offre du groupe s’adresse ainsi aux industries les plus variées, avec des points forts signalés par son dirigeant dans « la cosmétique, la pharmacie, la grande distribution, les pièces automobiles ou encore les fournitures de bureaux ». Pour un total installé d’un millier d’entrepôts. « Nous avons suivi la consolidation des acteurs dans les différentes filières que nous servons, ce qui nous amène à travailler avec des leaders mondiaux. Sans abandonner loin de là les acteurs de plus petite taille. Notre palette de contrats va de 250.000 à 30 millions d’euros », décrit Rémy Jeannin. Plus d’un projet majeur logistique situé dans le fief bourguignon de Savoye tombe dans son escarcelle, par exemple la prochaine plateforme de 13.000 m2 d’Urgo en périphérie de Dijon.
Au croisement de la data et de la robotique
Les mutations de l’intralogistique, Rémy Jeannin en identifie des facteurs multiples. L’automatisation, ainsi, ne cesse de gagner du terrain. Par une sorte de phénomène « naturel » de recherche d’efficacité et de productivité, « mais aussi par la difficulté généralisée de trouver la main d’œuvre ». Elle se double d’une interaction toujours plus forte avec le software. « Nous nous positionnons à la fois comme acteur de la data (sans être nous-mêmes éditeurs de base de données) et de la mécanique/robotique. Dans notre domaine, tracer une frontière entre ces deux fonctions n’a plus de sens », poursuit le dirigeant de Savoye.
De ce fait, l’entreprise côte-d’orienne se transforme en un « ensemblier », intervenant au stade de la conception des outils de pilotage comme les progiciels de WMS (Warehouse Management System) et d’OMS (Order Management System), de la fabrication, et donc de l’intégration. « Les clients attendent de plus en plus que nous sélectionnons avec eux les meilleurs process, à l’heure de l’accélération de l’innovation », observe le président de Savoye.
L’entreprise de référence de la gestion des flux opère sa propre modernisation, en conséquence. Au début de 2025, elle trouvera sa concrétisation majeure avec l’entrée en service, attendue pour cette échéance, de la nouvelle usine Savoye dans la zone Beauregard de Dijon. Sur une surface de 21.000 m2 et moyennant un investissement de 30 millions d’euros, le groupe y déploiera ses derniers équipements et moyens logistiques aujourd’hui situés à Ladoix-Sarrigny, et il y rassemblera également son siège. Le déménagement concerne un effectif de 500 personnes aujourd’hui, ayant vocation à croître.
Les ressources humaines, un défi de plus en plus multifacettes
Sur le thème des ressources humaines qui constitue le fil conducteur d’Euro Supply Chain 2024, Rémy Jeannin a sa vision, claire : là aussi, les mutations sont à l’œuvre et elles génèrent leurs défis. « Les tensions sur le marché de l’emploi étaient traditionnellement liées à l’activité des entreprises. C’est toujours le cas, mais elles se doublent de mutations plus profondes, qui ont trait à la quête d’équilibre entre la vie professionnelle et la vie privée. Pour une entreprise comme la nôtre, mondialisée, elles génèrent des enjeux particuliers. Comment rester attractifs dans les métiers de production ou de logistique comme les autres qui peuvent impliquer des déplacements longs par exemple ? Comment rester compétitif quand on travaille avec une région du monde comme l’Asie qui continue d’ériger le travail comme valeur suprême ? Nous y travaillons ».